Well suited to a warehouse operation looking to maximize storage space and create a very high density storage plan. In combination with solid warehouse management, Push Back Racking Systems can be an economical and efficient strategy.
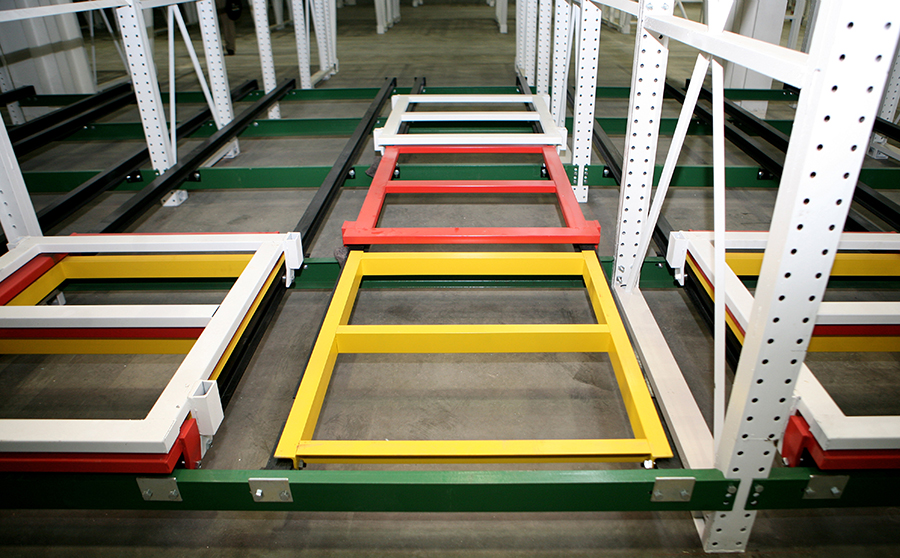
How it Works
- Racks are constructed on a gentle slope upward from the pick face
- Pallets rest on a cart system so as new pallets are added those already in are pushed back further
- As existing stock is pushed back the next cart in the system is available to receive
- Can be made up to six lanes deep with interlocking systems to deter jamming
The Good
- Extremely high density storage system
- Pick faces are always full and no special equipment is needed
- Well suited to Last-in-First-Out or First-In-First-Out if oldest lanes empty first
- Same density as Drive In Systems with more pick faces for improved stock access
- No need to drive into storage lanes means fork trucks stay in the main aisle reducing damage risk
- Less complexity and honey combing than Drive In Systems
- Increased efficiency and cost-savings due to reduced access times and handling of stock
Challenges to Overcome
- Must be structured to anticipate / accommodate varying operating loads
- Requires ongoing inspection and maintenance to ensure on-going reliable operation
- Needs strong warehouse management depending on rotation practices to plan slotting properly
Our Solutions
Racked Out can specify a variation of lane depths for your Push Back Racking System, typically from three to six lanes deep.
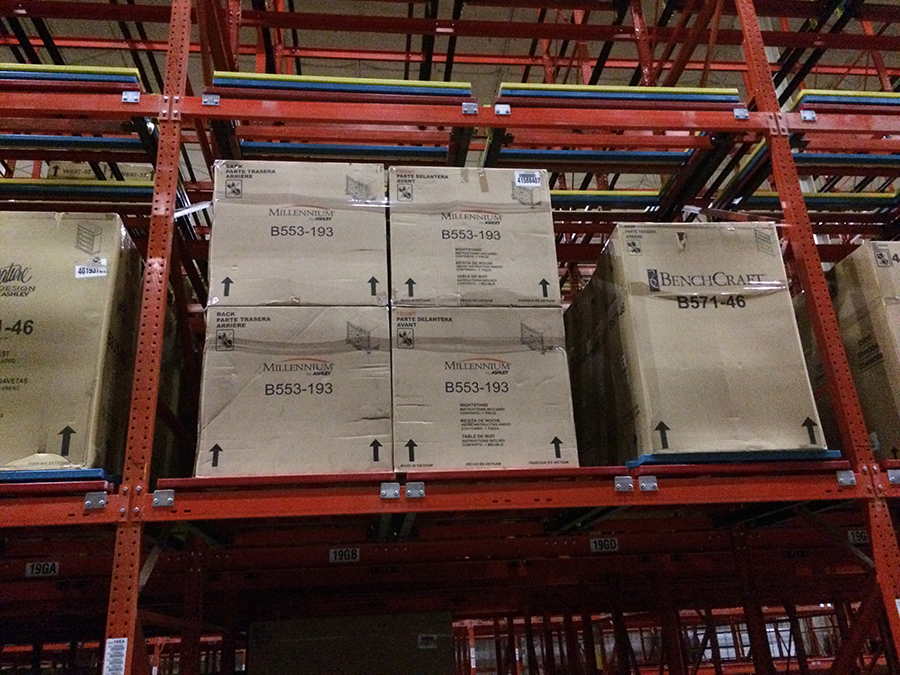
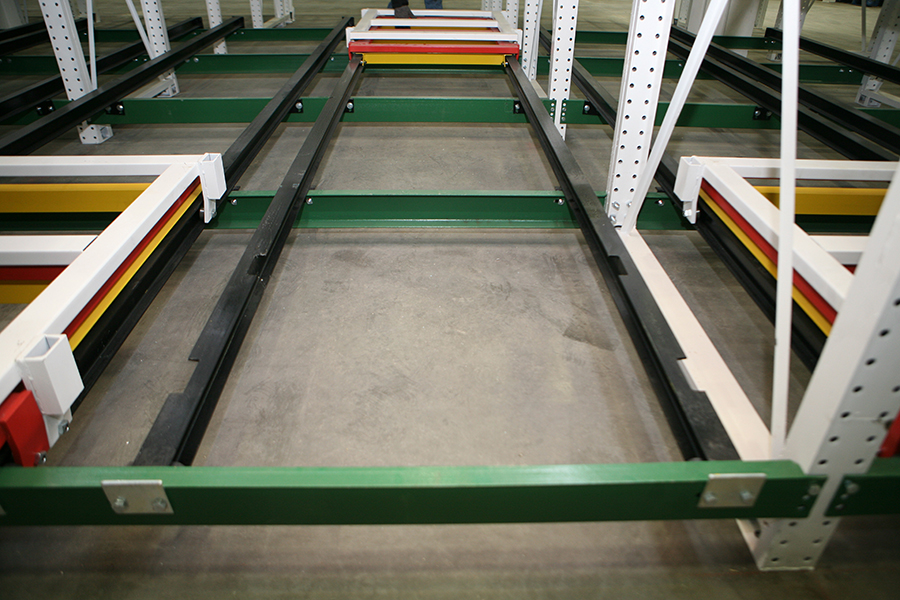
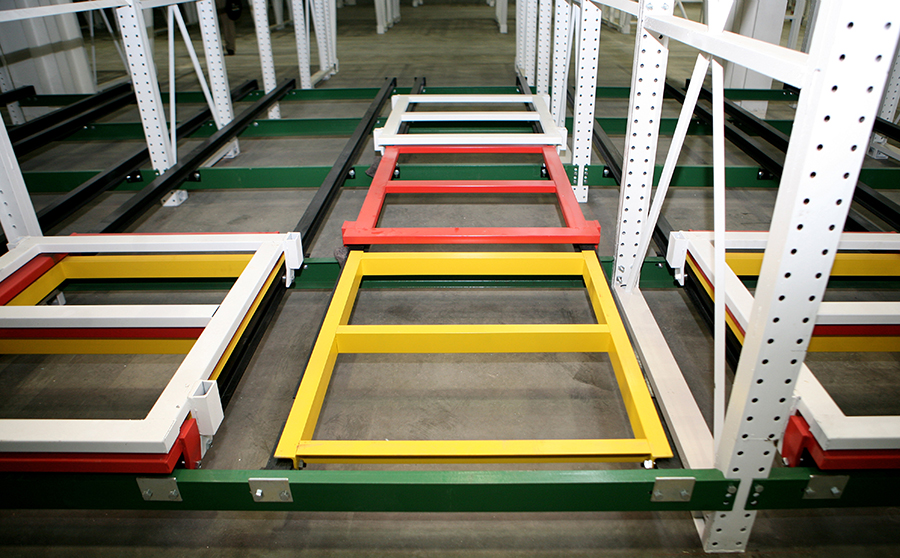
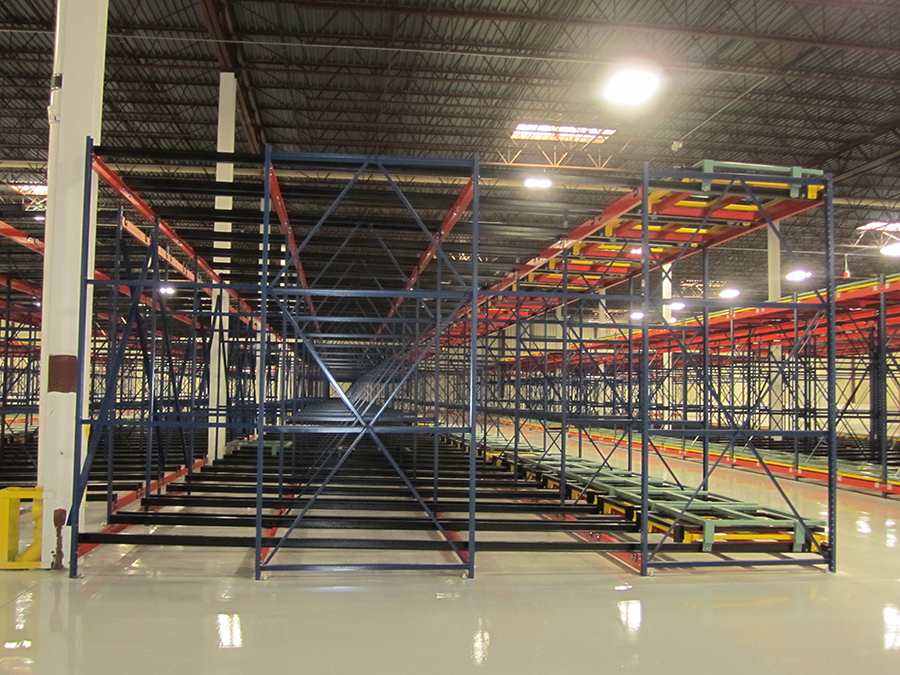
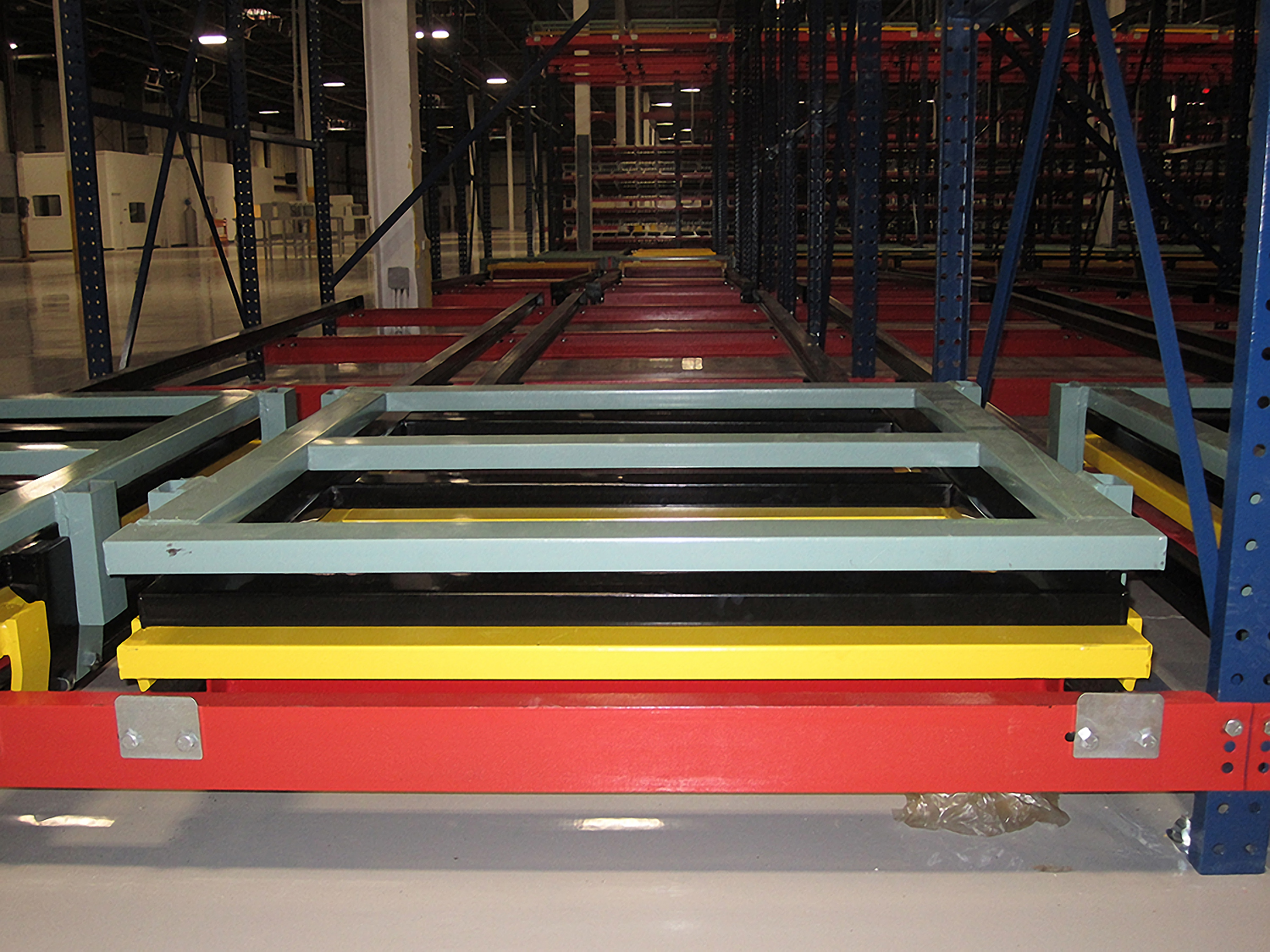