Compared to traditional racking setups using rows and aisles, drive-in racking increases storage density. A greater use of available floor area is realized and stores more product with less structure that can save operational costs.
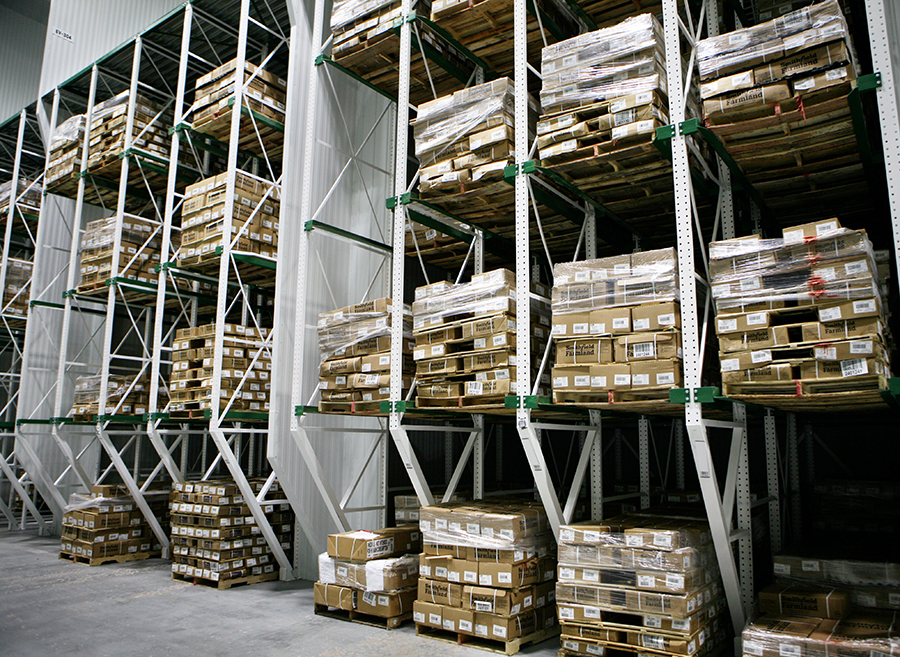
How it Works
- Lift truck enters the rack from one side
- Pallets slide backwards on a continuous rail two deep or more
- Depth of tunnels limited only by the facility size
The Good
- Much higher density makes it perfect for fast rotating stock with numerous pallets in same SKU
- Perfect for seasonal, single-load or breakable item storage
- Warehouse operates in a “last-in-first-out” stock rotation
- Bulk storage operations see increased in efficiency and cost savings
Challenges to Overcome
- Highest interaction between fork truck and rack structure
- Increase potential for damage as truck enters and operates between frames directly in the row
- Requires additional safety solutions including post-protectors, guide rails, setback frames
Our Solutions
Racked Out can create a drive-in racking solution perfect for your needs. Designing a custom solution takes into account products stored, stock rotation, gross floor area, safety and operational considerations.
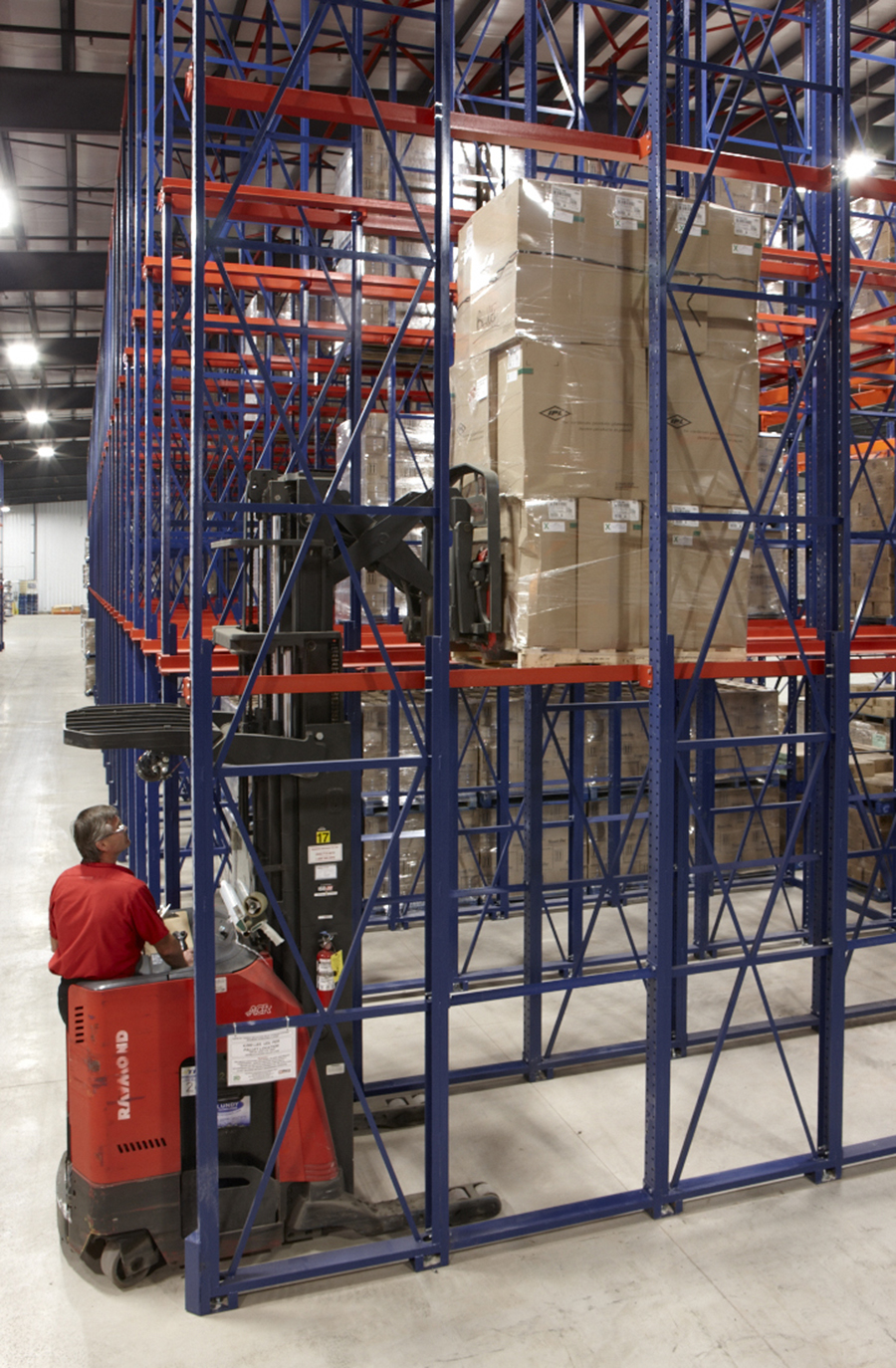
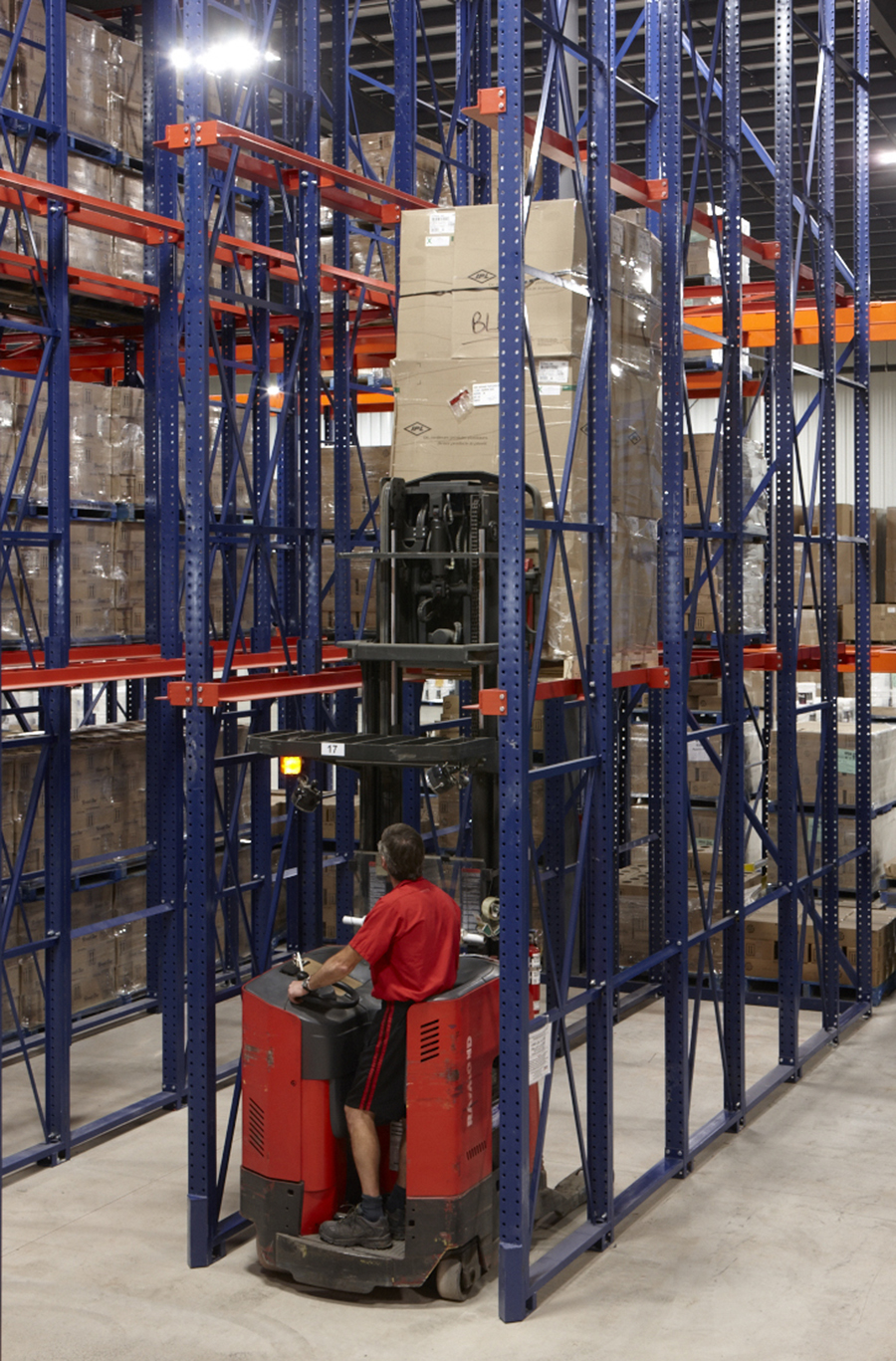
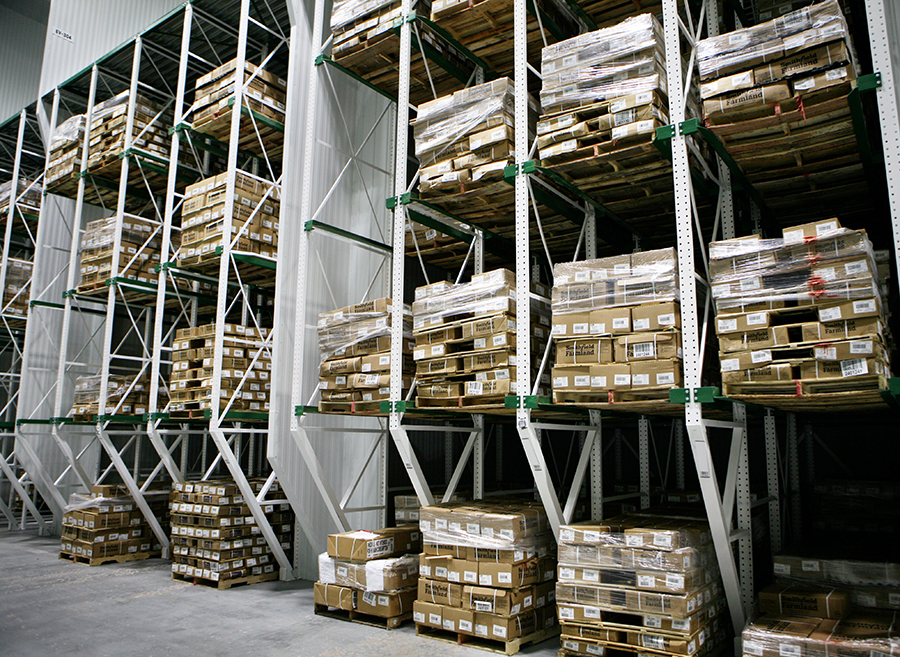
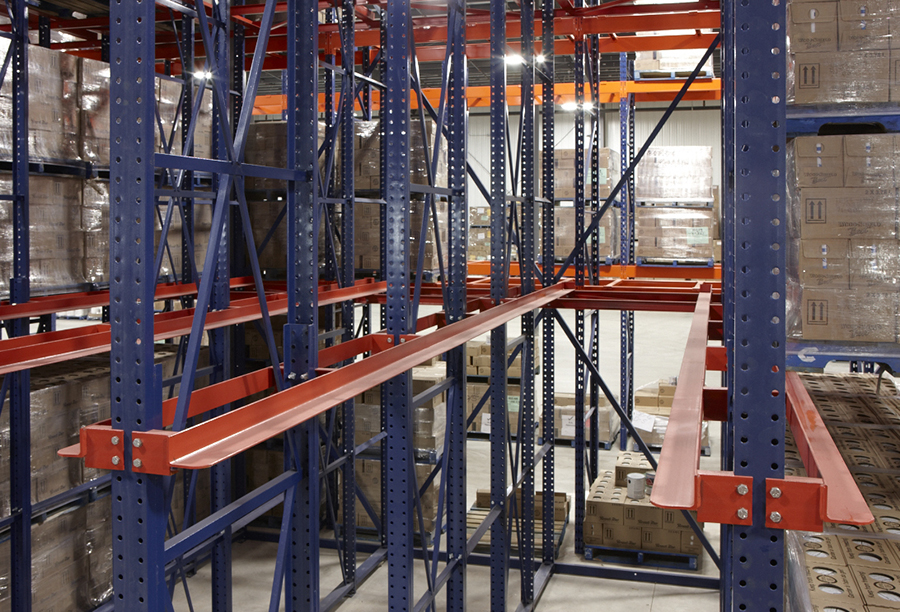
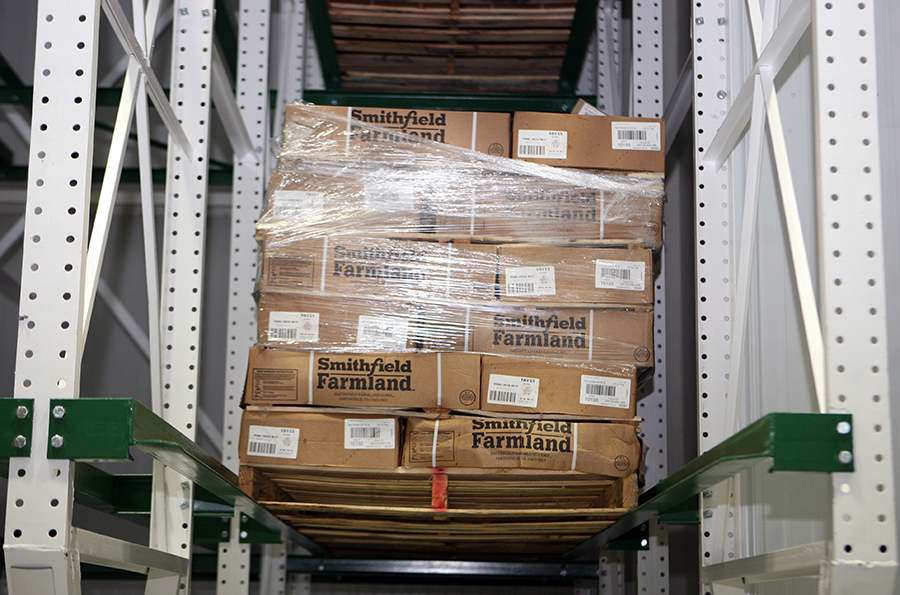